Christoph Henschel, BTU
In conventional architectural projects, the use of the building and the design concept typically determine the dimensions of the structure. This means that the height of spaces, as well as the width and length of rooms, are defined by what will happen in them once they are built. Constraints on the size of a building are usually only imposed by limited budgets, the site and its context, or zoning laws. All of this changes drastically when reused precast concrete comes into play. Suddenly, the structure dictates the spatial dimensions, the grid size or the floor heights of the building design. This changes the design task for the architect and presents new challenges. In order to show that these challenges are also full of opportunities, the following text describes the design process for the German pilot project within the ReCreate project, a youth center for the town of Hohenmölsen.
The design task began with a detailed analysis of the elements that could be salvaged from the donor building. Specific types, dimensions and available quantities of exterior and interior walls and ceiling slabs were determined. Preliminary tests of the concrete strength and examination of the reinforcement properties ensured the suitability for reuse in advance. With this catalogue of elements as a starting point, the design process for the new building could begin – always with the goal of using as many reused elements and as little new material as possible.

Resource: BTU Cottbus Senftenberg
The mayor of Hohenmölsen drew up a rough room plan that served as the basis for the initial design. It included a multi-purpose room, a kitchen and dining hall, several smaller rooms for offices or after-school use, and some additional rooms such as restrooms, storage, and a technical room. With these requirements in mind, an initial building layout sketch was created with the goal of locating the various uses in customizable areas of the future building. Conditions such as the distance from the entrance, the proximity of certain rooms to each other, or the orientation to the east, west, or south to ensure the best lighting were taken into account.
This initial sketch was then superimposed on a grid of 2.4m by 3.6m – the maximum length of the ceiling slabs in the donor building. After a few attempts and several iterations of rotating certain rows in the grid by 90°, two initial building designs were created and presented to the town of Hohenmölsen.
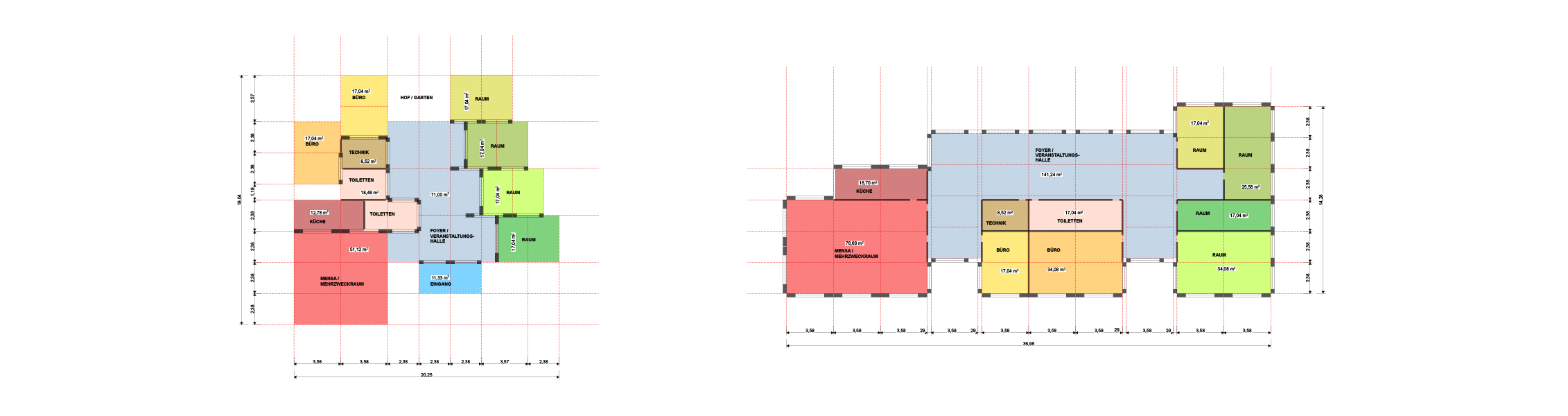
Resource: BTU Cottbus Senftenberg
A special design decision was to use the former exterior walls not only as exterior walls but also as interior walls in the new building to show that the building was created from reused elements. This also allowed for interior windows between two rooms, which was an interesting way to visually connect separate rooms.
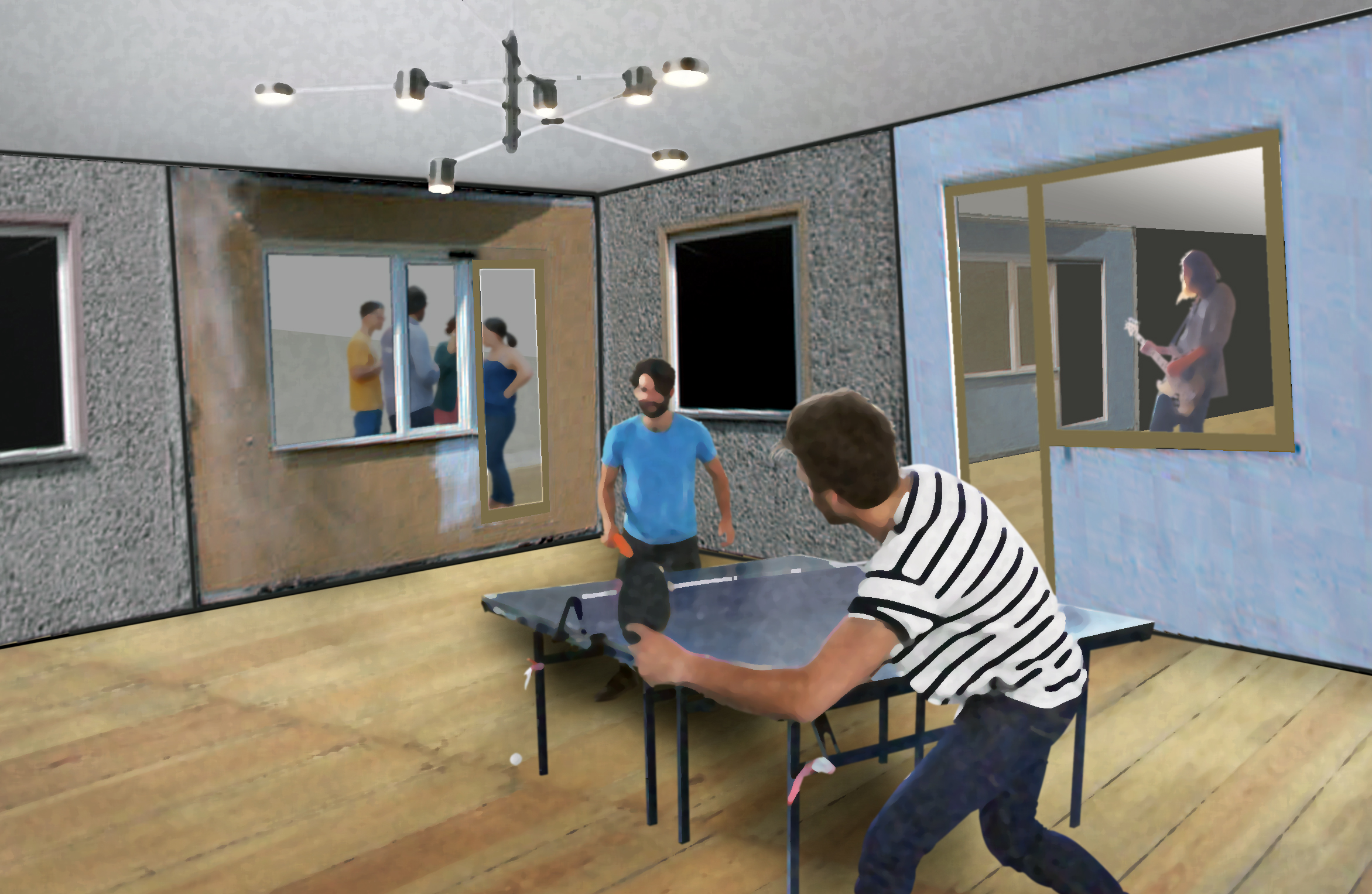
Resource: BTU Cottbus Senftenberg
The two initial building designs were presented by BTU at the town hall of Hohenmölsen and then discussed by the mayor with the town representatives. As a result of this discussion, BTU was asked to make a number of changes to the design in terms of size and use. This second design phase resulted in a combination of the two previous designs into one more detailed approach. In this design, it was already apparent that for the larger spaces, such as the dining room and multi-purpose room, the 3.6m ceiling spans were not sufficient, so new beams and columns were introduced to create wider spaces with double the span, resulting in a width of 7.2m. At this point, the method of showing reused elements in black lines and new material in red on the drawings was established. This allowed for a quicker overview of where reused elements would be located.
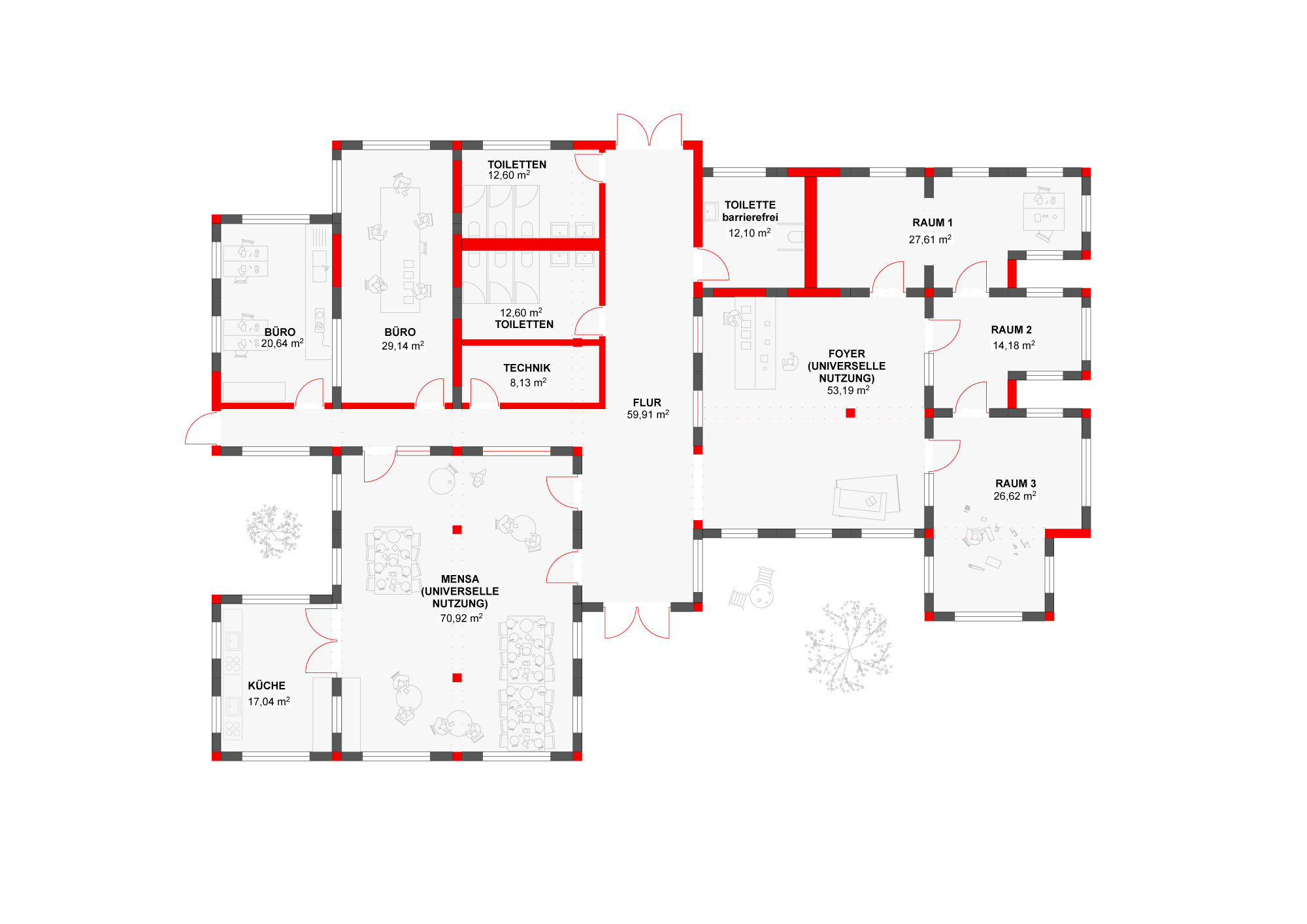
Resource: BTU Cottbus Senftenberg
During this design phase, the concept of multiple entrances to the building was developed, so that there is not just one main entrance, but several ways to approach the building, which can activate the building’s surroundings much better.
After another round of feedback from the town of Hohenmölsen, some minor changes were made and terrace roofs were added to the design. In this design, it is now possible to enter and exit the building from all four sides. This allows users to access the site from all sides. In this design, 47 used exterior walls, 7 used interior walls and 56 ceiling slabs are used.
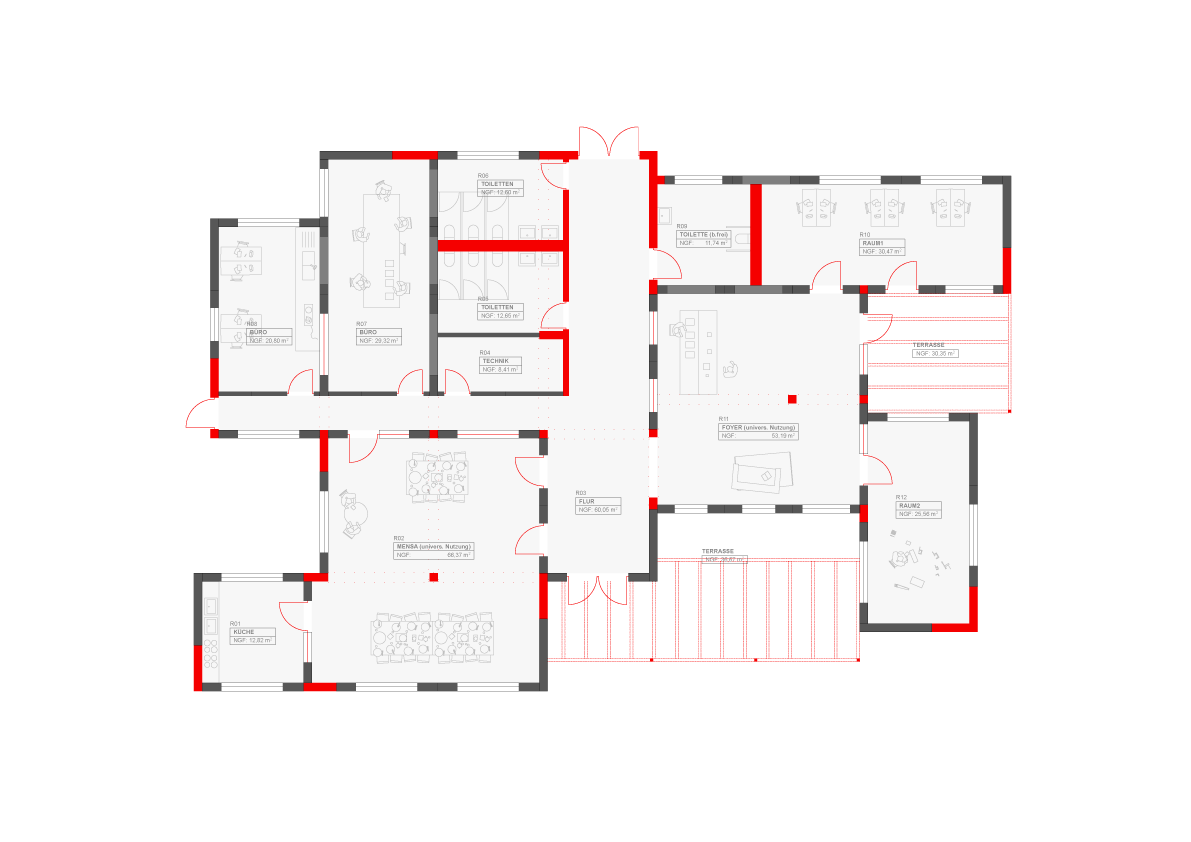
Resource: BTU Cottbus Senftenberg
Some time passed and the town of Hohenmölsen contacted BTU again, stating that the original space plan was not sufficient and that more space was needed. With the experience from the previous designs, a new layout was developed. The new design introduced the idea of a functional block with all building services such as kitchen, toilets, storage, etc., to be placed in the center of the building. This allows all the other rooms where youth activities or office work will take place to receive natural light.
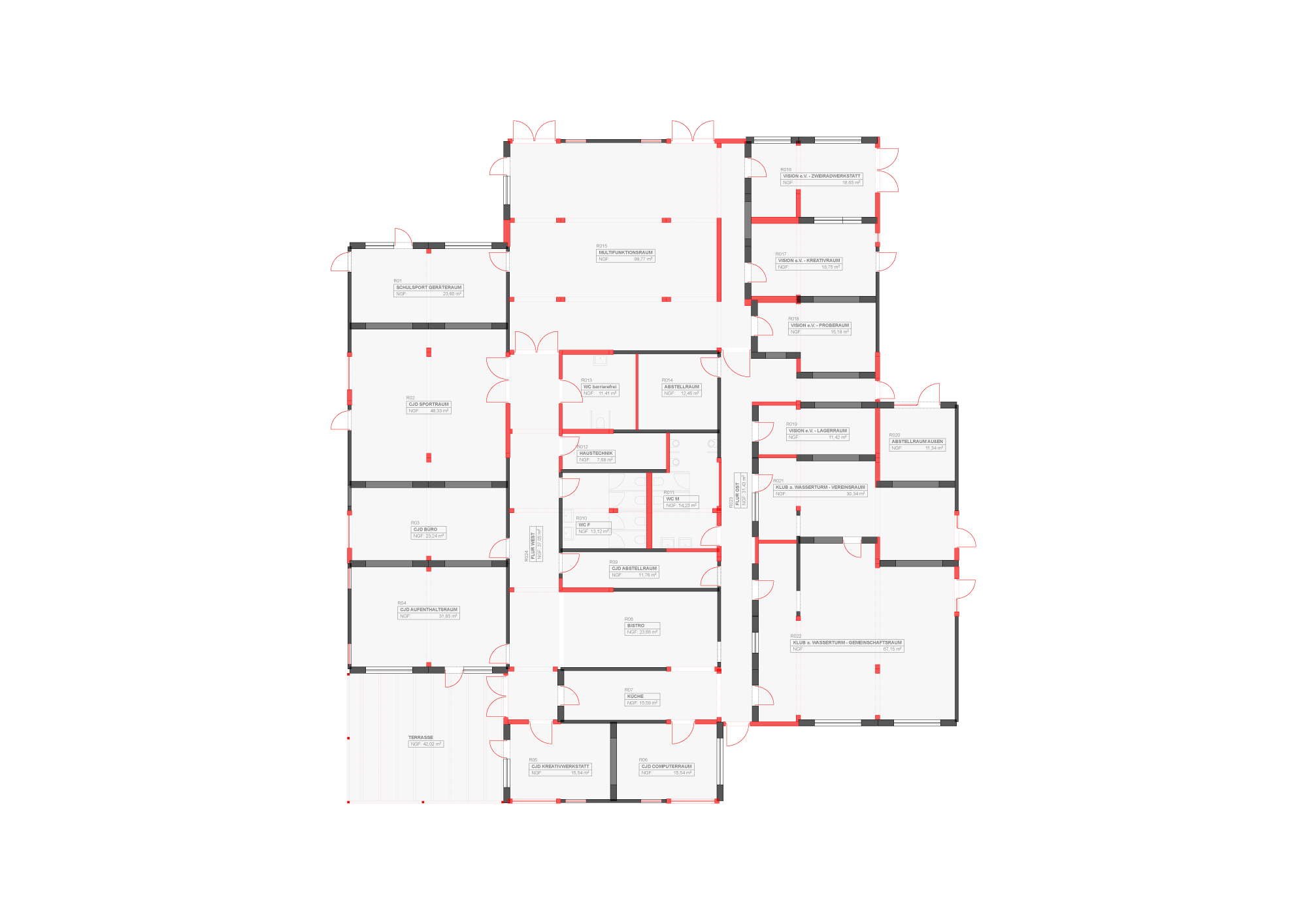
Resource: BTU Cottbus Senftenberg
The downside of this design was that it had a huge footprint of almost 700 m2 due to the increased space requirements. This led to the idea of arranging the spaces on two levels, creating a two-story building. The previous spatial configuration of a service core with a surrounding corridor and entrances on all four sides of the site was retained. Due to the peculiarities of the reused concrete elements and the limited grid size, it was decided that the upper floor would be accessed only by an exterior staircase to simplify the construction and avoid potential fire safety concerns.

Resource: BTU Cottbus Senftenberg
In this final design, 35 exterior walls, 25 interior walls and 103 floor slabs from the donor building will be reused, resulting in a net floor area of 505 m2 on the ground floor and 263 m2 on the upper floor. The new structural elements are initially planned to be new precast concrete elements such as columns and beams. New exterior and interior walls will be made of wood stud walls and ecological insulation such as wood fiber boards. For the facade, the reused exterior walls can be insulated with only 6 cm of wood fiber boards due to the low density concrete they are made of, while the reused interior walls, which will be positioned as new exterior walls, will require 14 cm of insulation. The façade will be a ventilated cladding of reused wood panels and reused corrugated metal, installed as available.
All in all, the design process was challenging, but also interestingly unusual, because the building elements determined many decisions that would otherwise have to be made by the architect or the client. Introducing new elements and rotating the grid in certain places allowed for some flexibility and gave just enough freedom to realize all the required uses in the building. The German ReCreate country cluster hopes to start construction of the youth center in late 2024 or early 2025.
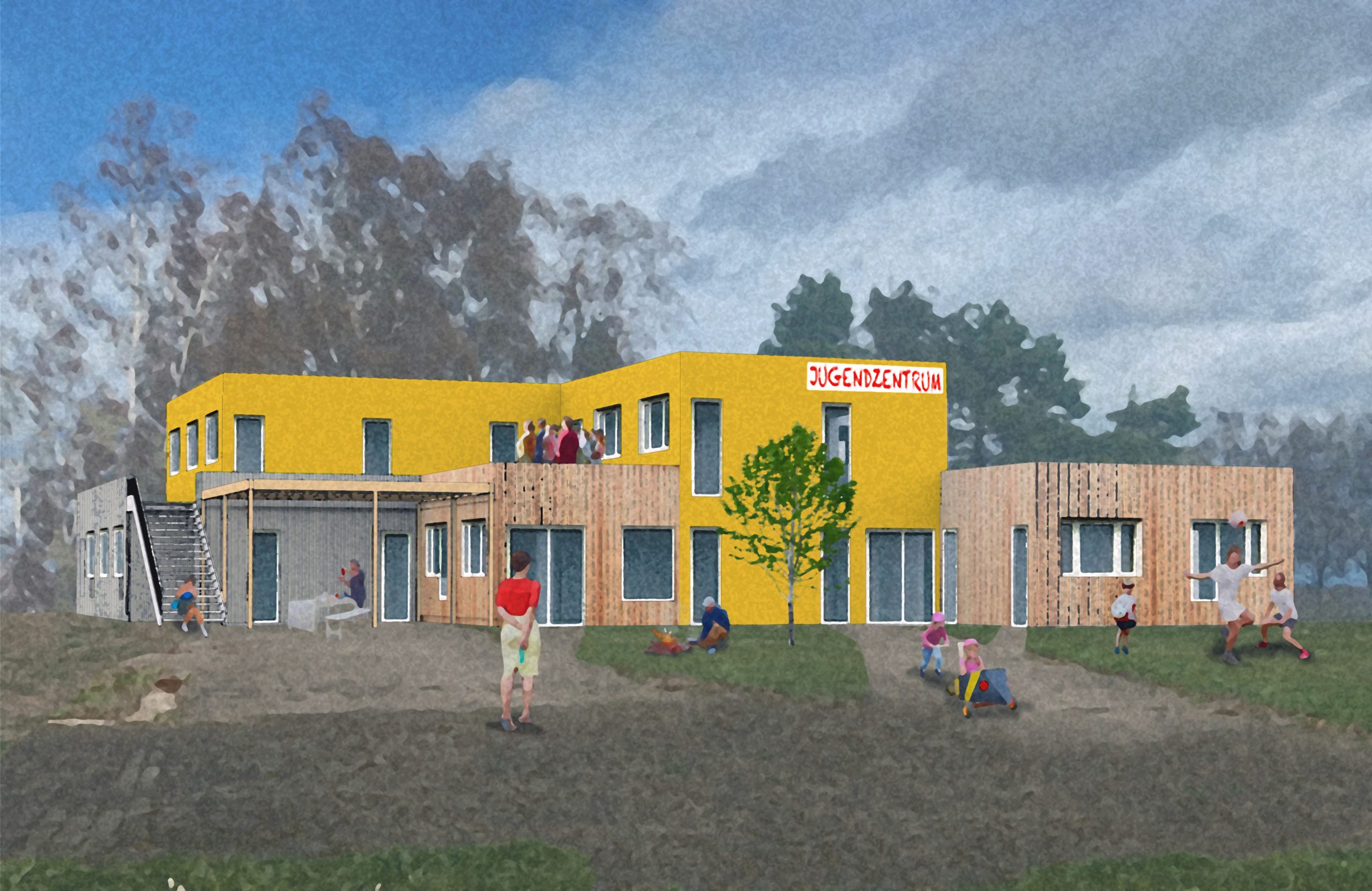
Resource: BTU Cottbus Senftenberg