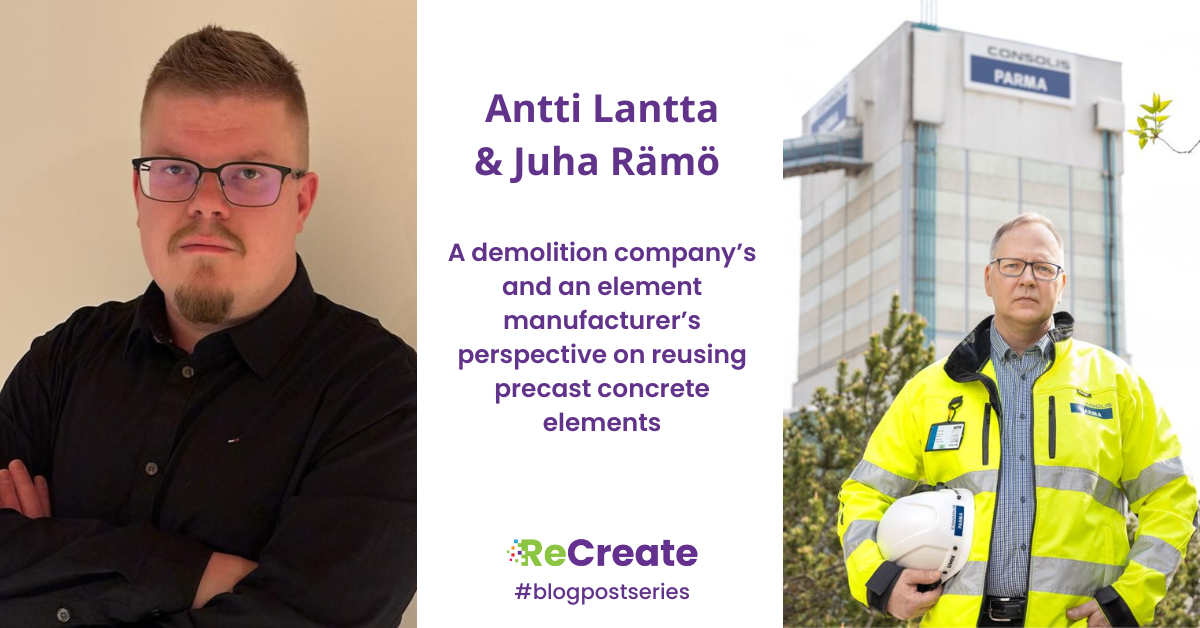
Antti Lantta, project manager (building demolition), Umacon & Juha Rämö, technology director, Consolis Parma
The earth’s carrying capacity is being tested, and it cannot sustain the growing use of virgin natural resources on the scale required by the current economic and population growth. The most acute environmental damage of our time results from global warming and the loss of biodiversity.
The built environment is of great importance for an ecologically sustainable society, as the construction sector globally consumes about half of all the world’s raw materials and causes about a third of greenhouse gas emissions. From the perspective of a circular economy, there is a huge potential here.
This includes the EU-funded four-year international research project ReCreate (Reusing prefabricated concrete for a circular economy), which studies the reuse of concrete elements, which are deconstructed from buildings slated for demolition, in new construction. Umacon, a top demolition expert, and Consolis Parma, Finland’s leading manufacturer of precast concrete elements, are also involved in the research project.
Umacon renews demolition industry in Finland
The prevailing demolition method in Finland focuses on material recovery, where the secondary raw material materials created through demolition are used in the recycled or otherwise utilized, for example in earthworks. Reusing whole precast concrete elements is rare, even though valuable building parts and equipment, such as building services components, industrial machinery and steel or wooden columns and beams, have been salvaged in Finland in the past. Until now, deconstruction has been driven more by the resale value of building components and equipment than the goal to reduce carbon dioxide emissions.
The reuse of precast concrete elements has not been implemented on a larger scale in Finland before. For Umacon, environmentally friendly and sustainable construction is part of its business values, so applying for the ReCreate research project was a natural choice. The work phases of the deconstruction project had to be planned in a new way so that the elements would not be damaged during the deconstruction work. During the project, new working methods and methods for detaching and lifting elements were developed to ensure that the deconstruction takes place safely and efficiently. Efficient working methods were refined as the project progressed. For example, it took four weeks to deconstruct the elements of the topmost floor, but the last floor was completed in just five working days! The key to a successful project was combining an array of different working methods that had been tried and tested in previous demolition projects into a functional deconstruction process.
Umacon wants to renew the demolition industry in Finland and become a leading company in the deconstruction sector. The success of the ReCreate research project shows that deconstructing precast concrete elements as intact is technically possible. By steering legislation towards low-carbon construction and improving the productivity of deconstruction, deconstruction will mainstream in Finland. Deconstruction and construction are teamwork that require the cooperation of all parties to achieve the goals.
New business for element manufacturer Consolis Parma
Consolis Group is committed to the targets set out in the Science Based Targets initiative. The Group’s global goal is to achieve zero emissions by 2050. The Finnish Consolis company Parma aims to reduce emissions by five per cent annually and halve them by 2035. The most significant means for reducing emissions are the increased use of low-carbon concrete elements, energy efficiency, and the circular economy.
Parma’s low-carbon products are based on substituting cement with binders from industrial side streams. In addition, crushed concrete is utilised in place of virgin aggregates. In the future, one possibility is to supply fully recyclable elements alongside new low-carbon concrete elements.
In the ReCreate research project, the reuse of whole elements is focused on in real life. The elements salvaged from the donor building in Tampere have been delivered to Parma’s Kangasala factory, where they undergo a quality check as well as the necessary modifications and equipment for reuse. The elements that have now been reclaimed were originally manufactured at the company’s factory in Ylöjärvi, Finland, and thus Parma is involved in a research project to promote the reuse of the elements it has manufactured itself.
In this kind of new business, the role of an element manufacturer may include, for example, design, quality control, dimensional changes and equipment, as well as other functions that are suitable to perform alongside new production at the precast concrete factory. Issues to be studied that deviate from new production include approvals, processes and logistics (deconstruction of elements, transfer to the factory, factory-refurbishment measures, transfer of elements to a new site and installation of elements) and environmental permit practices.
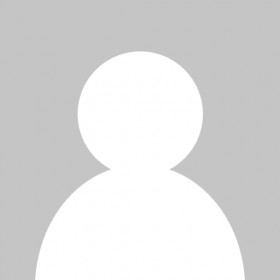